Appliquer un modèle industriel durable signifie adopter des processus de production et de gestion qui réduisent l’impact environnemental, optimisent l’utilisation des ressources et favorisent le bien-être social et économique à long terme.
Précurseur dans ce domaine, RIMSA a initié dès l’an 2000 un processus de numérisation qui s’incarne aujourd’hui dans un système de gestion intégré connectant l’homme et la machine de manière durable et responsable.
Modèle RIMSA
Industrie Durable
Numérisation: d’un outil applicatif à une culture d’entreprise
Comment l’Industrie 4.0 redéfinit les processus, les technologies et les méthodes dans un environnement de production intégré
Dans un contexte de transformation technologique et d’évolution des modèles de production, RIMSA a initié dès 2000 un parcours vers la digitalisation 4.0, anticipant les tendances du secteur.
L’introduction progressive d’outils opérationnels de pointe s’est progressivement intégrée aux valeurs et processus de l’entreprise, jusqu’à devenir une véritable culture d’entreprise : durable, responsable et tournée vers l’avenir.
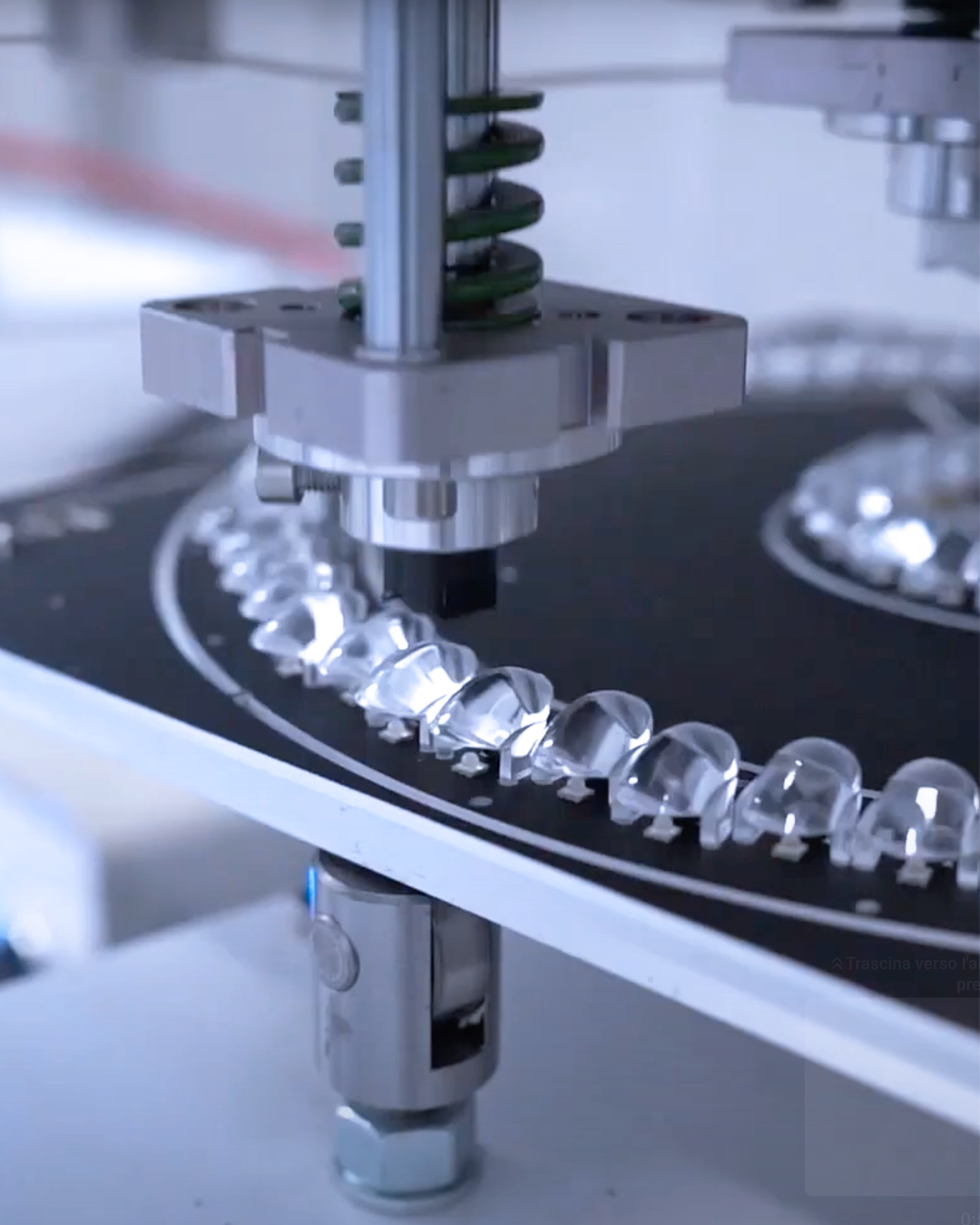
1
Fondamentaux de l’Industrie 4.0
Avec l’avènement de l’Industrie 4.0, les entreprises connaissent une profonde transformation qui touche les infrastructures, les systèmes de gestion et la culture organisationnelle.
Alors qu’autrefois l’automatisation se concentrait principalement sur la mécanisation et le contrôle des processus, l’innovation d’aujourd’hui concerne surtout l’intégration numérique des départements et la capacité à connecter machines, logiciels et personnes dans un écosystème unifié.L’Industrie 4.0 introduit plusieurs concepts clés: la digitalisation des flux d’information, l’interconnexion entre dispositifs et systèmes, l’intégration logicielle à tous les niveaux, l’analyse des données en temps réel, la maintenance et l’analyse prédictive, ainsi que la verticalisation des processus internes, visant à raccourcir la chaîne de valeur.
Dans cette optique, RIMSA est un exemple vertueux de la manière dont une PME peut entreprendre un parcours de digitalisation cohérent et approfondi, transformant en profondeur son modèle opérationnel.
2
Fondamentaux de l’Industrie 4.0
Les fondements de l’Industrie 4.0 reposent sur des concepts clés qui définissent l’évolution des processus de production vers un modèle toujours plus connecté, automatisé et intelligent.
Avant d’approfondir comment RIMSA incarne l’exemple d’une entreprise 4.0, voici quelques définitions de base.
Digitalisation
Digitaliser ne signifie pas simplement remplacer le papier par des fichiers numériques, mais redessiner l’ensemble des processus en exploitant des données en temps réel et des logiciels de plus en plus performants.
Chez RIMSA, cela se traduit par une gestion intégrée des flux de projet, de production et de logistique, où les systèmes communiquent et partagent automatiquement les informations.
Interconnexion
La véritable force de l’Industrie 4.0 réside dans la capacité à connecter machines, capteurs, logiciels et personnes dans un réseau intelligent.
Chaque élément fournit et reçoit des données, permettant une prise de décision rapide et efficace.
Par exemple, une machine de peinture peut transmettre en temps réel au système de gestion les écarts de production ou les besoins de maintenance, tandis que les départements conception, qualité et production restent constamment synchronisés.
Intégration (des logiciels)
L’intégration logicielle crée un écosystème numérique où CRM, ERP, MRP, PLM, CAM et outils de Business Intelligence interagissent de manière fluide.
Cela élimine les silos d’information entre services.
Chez RIMSA, par exemple, un modèle 3D est chargé dans le PLM, accessible au contrôle qualité et à la production, et interconnecté au MRP pour mettre à jour automatiquement les cycles de travail et nomenclatures.
Analyse de données
Les données sont le moteur de l’Industrie 4.0.
Leur collecte, traitement et interprétation en temps réel permet des décisions fondées sur des faits, et non sur des hypothèses.
De la production aux ventes en passant par les stocks et la traçabilité, les informations alimentent un système de KPI clairs pour suivre l’efficacité opérationnelle.
Analyse prédictive
Allant au-delà de la Business Intelligence, l’analyse prédictive permet d’anticiper les événements futurs.
Grâce à l’intelligence artificielle ou à des algorithmes statistiques, il est possible de prévoir les besoins de maintenance ou les pics de demande.
Chez RIMSA, cette approche réduit les arrêts imprévus et optimise les ressources.
Verticalisation
La verticalisation des processus consiste à internaliser certaines étapes de production ou de conception pour renforcer le contrôle sur la qualité et les délais.
Dans une logique 4.0, il ne s’agit pas seulement de “tout faire en interne”, mais de gérer chaque étape avec traçabilité et transparence.
RIMSA intègre ainsi certaines opérations tout en collaborant étroitement avec des fournisseurs fiables, capables de partager rapports et tests qualité.
3
Contrôle et traçabilité: Les avantages de l’Industrie 4.0 pour les entreprises
Un système entièrement digitalisé permet de savoir à tout moment où se trouvent les matériaux, l’état d’avancement d’une commande ou les tests réalisés sur un composant.
Réduction des coûts et des déchets
La digitalisation rend les processus plus fluides, élimine les étapes inutiles et évite les doublons.
Une meilleure planification optimise l’usage des ressources (matières premières, temps, personnel).
Chez RIMSA, l’optimisation des cycles de production et la gestion synchronisée des stocks via le MRP réduisent les surplus et les productions inutiles.
Le Passeport Numérique
Chez RIMSA, chaque pièce produite reçoit un passeport numérique, qui regroupe les données de fabrication, les numéros de série des composants, les tests effectués et leurs résultats. En cas de non-conformité d’un composant, son origine est immédiatement traçable, ce qui améliore considérablement le time-to-resolution..
Efficacité énergétique
Avec l’Industrie 4.0, la durabilité devient un élément central.
L’analyse en temps réel des consommations et l’usage de technologies intelligentes permettent une gestion énergétique rationnelle.
En cas de baisse de charge, les lignes sont ralenties ou arrêtées automatiquement.
Les émissions de CO₂ sont également suivies, avec la possibilité d’activer des stratégies de compensation.
Durabilité sociale
Un environnement numérique est aussi plus motivant.
Des interfaces intuitives, des processus clairs et la formation continue favorisent l’engagement et l’évolution des compétences.
Grâce à la plateforme LMS, RIMSA permet à ses collaborateurs de se former en continu et de changer de poste plus facilement au sein de l’entreprise.
Amélioration de la qualité
Dans un système connecté, la qualité est contrôlée à chaque étape.
Les rapports sont automatiquement liés au numéro de série du produit.
Grâce à l’intégration entre modèles 3D, PLM et logiciels de mesure, les erreurs sont évitées et chaque mise à jour est immédiatement prise en compte avant la mise en production.
4
La digitalisation en action : l’exemple de RIMSA
Entreprise historique spécialisée dans l’éclairage professionnel, RIMSA a entamé un processus de digitalisation étendu à tous les départements.
Cette transformation s’est construite progressivement, à travers une vision claire et des investissements constants en logiciels, machines et formation.
Du bureau technique à la production
Chez RIMSA, le dessinateur conçoit un modèle 3D via un logiciel CAD avancé.
Le fichier est chargé dans le PLM et devient accessible au service qualité, aux achats et à la production.
Grâce à une personnalisation logicielle, le responsable qualité insère directement les tolérances à vérifier pour chaque phase (réception, pré-usinage, post-usinage).
L’ERP/MRP, intégré au PLM, met automatiquement à jour les plans de contrôle et les instruments de mesure, sans saisie manuelle.
Interaction Homme-Machine et Contrôle CAM
L’un des piliers de l’Industrie 4.0 est l’interaction directe entre les personnes, les machines et les systèmes.
Chez RIMSA, les machines-outils récupèrent les programmes d’usinage directement depuis le PLM de l’entreprise.
Si un concepteur met à jour un projet, la machine compare la version du dessin avec celle du programme CAM : en cas de divergence, elle bloque la production jusqu’à ce que le responsable CAM publie la bonne version. Cela réduit considérablement les erreurs dues à des incohérences entre conception et programmation.
Logistique interne, nomenclatures et gestion des stocks
La digitalisation concerne aussi la logistique interne : la nomenclature de chaque produit comprend non seulement les composants, mais aussi les étapes de fabrication et les besoins associés.
Dès qu’une phase est lancée, le système de gestion envoie un ordre de prélèvement au magasin, indiquant les quantités exactes à préparer et le moment opportun.
Cela améliore l’organisation et la clarté pour les opérateurs, qui peuvent composer leur chariot de travail de manière séquentielle, sans déplacements inutiles.
Postes de travail “intelligents” et formation continue
Chaque opérateur de la ligne de production dispose d’une tablette permettant l’accès aux informations nécessaires : visualisation 3D, fiches de montage, disponibilité des matériaux.
En cas de doute, il peut consulter en temps réel la plateforme LMS de l’entreprise, visionner des tutoriels sur les étapes d’assemblage, ou se former à d’autres processus.
Cette ouverture favorise l’acquisition de nouvelles compétences et la mobilité interne, horizontale comme verticale.
Traçabilité totale et passeport numérique du produit
Chez RIMSA, chaque machine de test génère un rapport numérique lié au lot ou au numéro de série du composant.
Chaque transformation majeure est associée à un numéro unique, intégré ensuite dans celui du produit fini.
À partir d’un simple numéro de série, l’entreprise peut retrouver en quelques secondes l’ensemble des tests et leurs résultats, ainsi que les composants utilisés.
Cette traçabilité complète est précieuse aussi en après-vente, garantissant que toute pièce de rechange corresponde exactement aux spécifications d’origine.
KPI e JIT
Une fois les données partagées de manière fluide entre les départements, il devient simple de suivre des indicateurs clés comme la productivité, les arrêts machines, le rendement individuel ou les non-conformités.
Le Just In Time, qui consiste à produire uniquement quand c’est nécessaire, s’appuie sur une planification en temps réel, réduisant les stocks et accélérant les délais de livraison.
Collaboration avec les Fournisseurs
Chez RIMSA, la qualité dépasse les frontières de l’entreprise : les fournisseurs doivent suivre les mêmes protocoles de transparence.
Pour chaque composant, ils génèrent des rapports de test complets, intégrés aux archives numériques de l’entreprise.
Cela permet une gestion intégrée des partenaires, dont les processus doivent refléter les standards élevés de RIMSA.
5
Les « mots-clés » de la numérisation en entreprise
Voici quelques mots-clés qui représentent les piliers de la numérisation en entreprise et illustrent concrètement la manière dont RIMSA applique l’innovation numérique à ses processus internes, en valorisant l’efficacité, la durabilité et la responsabilité.
1. CRM (Customer Relationship Management) ↓
Le CRM est l’outil qui permet à l’entreprise de gérer ses relations avec les clients et prospects.
Dans le cadre de l’Industrie 4.0, il devient l’interface entre les besoins du marché et les fonctions internes, permettant de proposer des offres personnalisées, d’améliorer le service client et d’optimiser les actions marketing.
Un CRM moderne ne se limite pas à une base de données : il intègre des informations issues de plusieurs canaux (email, réseaux sociaux, e-commerce), offrant une vue client à 360°.
L’équipe commerciale ou SAV peut ainsi accéder à des données actualisées en temps réel pour offrir une réponse rapide et cohérente.
Le CRM permet également d’automatiser les processus, d’analyser les comportements d’achat, de segmenter la clientèle et de planifier des campagnes ciblées. Il interagit avec les autres systèmes (ERP, PLM…), facilitant la vérification de la disponibilité produit, la personnalisation d’une commande ou le suivi d’un projet.
La verticalisation des processus, rendue possible grâce au CRM, permet de réduire la distance entre ceux qui interagissent avec le marché et ceux qui fabriquent physiquement le produit.
Lorsqu’un client soumet une demande, il est possible de vérifier en quelques clics l’état d’avancement de la commande ou d’une éventuelle réclamation, en reliant ces informations au système de gestion de la qualité.
En résumé, le CRM agit comme un véritable “tableau de bord relationnel”, mettant le client au centre de la stratégie et renforçant la réputation de l’entreprise dans un écosystème connecté.
2. ERP (Enterprise Resource Planning) ↓
L’ERP (Enterprise Resource Planning) est le cœur névralgique de nombreuses entreprises, car il coordonne l’ensemble des flux d’informations à caractère économique et administratif.
Il permet de gérer les commandes, la facturation, la comptabilité, les fiches produits et de stock, la planification de la production, et bien plus encore.
Dans le contexte de l’Industrie 4.0, l’ERP devient un nœud d’intégration essentiel, recevant et transmettant des données vers le CRM, le MRP, le PLM et tout autre logiciel de l’entreprise.
L’une des grandes évolutions de l’ERP à l’ère numérique est sa modularité : les entreprises peuvent choisir les modules les plus adaptés à leurs besoins, et les intégrer via des API ou des connecteurs standards.
Ainsi, on évite les doublons et on garantit un alignement constant des informations.
Par exemple, une commande client saisie dans le CRM est automatiquement transmise à l’ERP pour vérification des stocks et génération de la nomenclature, sans intervention manuelle.
Un ERP bien structuré fournit des données en temps réel sur la situation financière et logistique de l’entreprise, améliorant la prise de décision basée sur des KPI fiables.
Grâce à l’analyse prédictive, il devient possible d’estimer les flux de trésorerie futurs, de planifier des investissements ou d’évaluer la rentabilité de projets spécifiques.
Chez RIMSA, l’ERP constitue le point central reliant le service achats, l’entrepôt et la production :
lorsqu’un ordre de fabrication est lancé, l’ERP informe le stock des matières premières à prélever et actualise en parallèle les besoins futurs selon les prévisions de vente.
En cas de modification d’un dessin technique, l’ERP interagit avec le PLM et le MRP pour refléter les nouvelles spécifications en temps réel.
L’adoption d’un ERP intégré permet ainsi d’assurer contrôle, transparence et rapidité d’exécution, tout en réduisant les erreurs liées aux procédures manuelles ou aux lacunes de communication entre les services — des éléments clés pour toute entreprise visant l’excellence opérationnelle.
3. MRP (Material Requirements Planning) ↓
Le MRP (Material Requirements Planning) est le système qui permet de calculer les besoins en matériaux et composants en fonction des plans de production et des prévisions de vente.
Il s’agit d’un outil fondamental dans une optique Industrie 4.0, car il permet un contrôle rigoureux des stocks, évitant à la fois les excédents inutiles et les ruptures qui pourraient bloquer la production.
Sur le plan fonctionnel, le MRP lit les ordres de fabrication et les nomenclatures de chaque article. En croisant ces données avec les niveaux de stock disponibles, il calcule automatiquement les quantités de matières premières et de produits semi-finis à acheter ou à fabriquer.
Dans une entreprise connectée, ce processus est entièrement intégré à l’ERP, au PLM et aux modules de production, éliminant les tâches manuelles et réduisant les risques d’erreur.
Un MRP avancé gère également les délais d’approvisionnement, les lots minimaux et les stocks de sécurité, contribuant ainsi à l’optimisation des stratégies d’achat et de fabrication.
Par exemple, si un composant a un délai d’approvisionnement de 4 semaines, le système planifie automatiquement la commande à l’avance, évitant tout retard.
La verticalisation des processus – lorsqu’une entreprise décide d’internaliser certaines opérations – exige également que le MRP soit capable de gérer la disponibilité des machines et du personnel, en plus des matériaux.
Chez RIMSA, le MRP joue un rôle central dans la réduction des déchets et dans l’atteinte du Just In Time (JIT) :
lorsqu’une commande entre dans le système, le MRP coordonne les différents services, détermine quels composants doivent être produits en interne et lesquels achetés à des fournisseurs, et dans quels délais.
En cas de modification d’un dessin technique, le MRP met à jour automatiquement la nomenclature et les spécifications d’approvisionnement, en communiquant les changements au stock et au service achats.
Au-delà de la planification, le MRP alimente également les processus en aval tels que la planification des opérations et les contrôles qualité.
Dès qu’un bon de commande est généré, l’équipe qualité est automatiquement alertée sur l’arrivée des matériaux, ce qui garantit que le contrôle à la réception est prêt.
Grâce à cet environnement numérique interconnecté, les erreurs sont détectées en amont et les données essentielles sont enregistrées automatiquement.
En définitive, le MRP aligne les niveaux de stock sur les besoins réels de production, soutenant les objectifs du lean manufacturing.
La planification automatisée en temps réel permet de réduire les surplus, accélérer les délais de production et renforcer la fiabilité — des piliers fondamentaux pour une entreprise performante dans l’Industrie 4.0.
4. PLM (Product Lifecycle Management) ↓
Le PLM (Product Lifecycle Management) est la plateforme qui gère l’ensemble du cycle de vie d’un produit, de la phase de conception à la production, en passant par la distribution et la fin de vie.
Dans le contexte de l’Industrie 4.0, le PLM devient une sorte de référentiel central pour toutes les informations et révisions liées aux produits de l’entreprise.
Concrètement, le PLM stocke les modèles 3D, les nomenclatures, les spécifications techniques, ainsi que la documentation de tests et les certifications.
Toute modification d’un dessin, d’une cote ou d’un matériau est enregistrée en temps réel, générant une nouvelle révision qui est automatiquement propagée aux autres systèmes connectés, comme l’ERP ou le MRP.
Cela permet d’éviter les erreurs typiques d’une gestion analogique, telles que les fichiers obsolètes ou les instructions ambiguës.
Un PLM moderne intègre également des fonctionnalités de collaboration et de gestion des flux de travail, permettant aux concepteurs, responsables qualité, équipes de production et autres fonctions de travailler ensemble sur un même projet.
Par exemple, le service qualité peut ajouter des tolérances et des plans de contrôle directement sur le modèle 3D, tandis que les concepteurs reçoivent des notifications en temps réel concernant les demandes de modification.
Dans le cas de RIMSA, le PLM a été personnalisé pour intégrer les données du contrôle qualité (QA), de la programmation CAM et du MRP.
Lorsqu’un concepteur modifie un dessin, le logiciel alerte immédiatement le responsable CAM, qui met à jour le programme machine.
Si ce dernier ne correspond pas à la dernière révision du dessin, la machine-outil bloque automatiquement l’usinage, évitant ainsi tout défaut de production.
Ce niveau d’interconnexion et de traçabilité permet de créer un véritable “passeport numérique” pour chaque produit, dans lequel sont enregistrées toutes les informations critiques — des spécifications de conception aux tests finaux — apportant à l’entreprise un avantage concurrentiel considérable en termes de qualité et de service client.
5. Cloud ↓
Le Cloud représente aujourd’hui l’infrastructure clé de l’Industrie 4.0.
Plutôt que de maintenir des serveurs physiques en interne, le cloud permet de tirer parti de ressources informatiques à distance, offrant ainsi plus de scalabilité, de fiabilité et de sécurité.
Les plateformes cloud facilitent également l’interconnexion entre les différents services et avec les fournisseurs, en permettant un accès aux données depuis n’importe quel endroit et appareil, sous réserve d’une connexion Internet stable.
Pour une entreprise comme RIMSA, la transition vers le cloud signifie la possibilité d’intégrer tous les systèmes (CRM, ERP, MRP, PLM, LMS) dans un environnement unifié, sans se soucier des infrastructures matérielles.
Cette approche simplifie les mises à jour logicielles, qui se font de manière automatique et transparente pour les utilisateurs finaux, et garantit des systèmes de sauvegarde et de reprise après sinistre plus robustes que les solutions “on-premise”.
Para una empresa como RIMSA, migrar al Cloud significa integrar sistemas como CRM, ERP, MRP, PLM y LMS en un entorno unificado, sin preocuparse por el hardware.
Esto facilita las actualizaciones automáticas, garantiza copias de seguridad seguras y planes de recuperación ante desastres más sólidos que las soluciones on-premise.
D’un point de vue collaboratif, le cloud permet aux collaborateurs de partager rapidement des documents, des dessins et des rapports avec des collègues, des partenaires ou des clients, et même de travailler simultanément sur un même fichier.
Dans le cadre de projets IoT (Internet of Things), les données générées par les capteurs et les machines sont envoyées en temps réel vers des serveurs distants, où des algorithmes d’analyse prédictive peuvent traiter des modèles complexes.
En résumé, l’adoption du cloud n’est plus un luxe, mais un élément fondamental de toute stratégie Industrie 4.0, car elle rend la digitalisation plus agile, plus économique et plus sécurisée.
6. Verticalisation des Processus ↓
La verticalisation des processus, dans une logique Industrie 4.0, consiste à internaliser certaines phases de production ou de développement, afin de réduire la dépendance vis-à-vis des fournisseurs externes et de renforcer le contrôle sur les délais, les coûts et la qualité.
Il ne s’agit pas de fermer la chaîne de valeur, mais de la structurer intelligemment, pour que la valeur ajoutée reste au sein de l’entreprise, tout en assurant que les partenaires externes soient intégrés numériquement au même niveau que les services internes.
Chez RIMSA, la verticalisation s’est concrétisée par l’internalisation de plusieurs étapes de production, de la conception jusqu’à la peinture et aux tests finaux, en intégrant machines-outils et logiciels de gestion au sein d’une plateforme numérique unifiée.
Ce choix stratégique permet de raccourcir la chaîne logistique, de réduire les délais de livraison et de rendre l’entreprise moins vulnérable aux retards ou inefficacités de tiers.
Un autre avantage essentiel de la verticalisation est la traçabilité de bout en bout : en gérant chaque étape en interne, l’entreprise bénéficie d’une vision complète du processus.
Par exemple, lorsqu’un composant nécessite une opération spéciale (tournage, fraisage, peinture), RIMSA peut planifier cette phase via le MRP, la réaliser sur une machine CNC interconnectée, puis enregistrer les résultats des tests dans le PLM, sans rupture d’information.
Cela améliore aussi la qualité, puisque les contrôles peuvent être effectués sur place et à plusieurs reprises, intégrés directement dans le flux de production.
Cette stratégie n’exclut pas la collaboration avec des fournisseurs externes, mais les intègre dans un système partagé, fondé sur le respect strict des exigences et des spécifications.
En définitive, la verticalisation à l’ère de l’Industrie 4.0 maximise l’efficacité, la transparence et la capacité d’adaptation face aux exigences du marché, en favorisant une relation directe entre conception, production et client final.
7. Du Bureau Technique à la Machine – Modèle 3D, Contrôle Qualité et CAM ↓
L’un des exemples les plus marquants de l’intégration Industrie 4.0 est la communication fluide entre la conception, le contrôle qualité et la production.
Imaginons le scénario dans lequel un concepteur de RIMSA crée un modèle 3D d’un nouveau composant.
Ce fichier, enregistré dans le système PLM, devient immédiatement accessible au responsable qualité, qui y ajoute les tolérances et les paramètres de contrôle à différentes étapes (réception matière, pré-usinage, tests finaux), le tout sur le même dessin numérique.
Le PLM notifie ensuite automatiquement le MRP, qui met à jour les besoins en matériaux et les cycles de fabrication.
Si le composant nécessite un usinage CNC, le responsable CAM élabore le programme machine, en vérifiant que la révision du dessin correspond bien à celle du fichier CAM.
C’est ici qu’intervient l’interaction homme-machine : la fraiseuse télécharge le programme directement depuis le PLM.
En cas de divergence entre la version du dessin et celle du programme CAM, la machine bloque automatiquement la production, signalant une erreur de version. La fabrication ne redémarre que lorsque le fichier CAM est corrigé et validé.
En parallèle, le responsable qualité peut définir les mesures à vérifier en ligne, en chargeant les valeurs et tolérances dans les systèmes de métrologie connectés.
Ainsi, les opérateurs ne saisissent plus manuellement les données, évitent les erreurs et travaillent toujours avec des informations à jour.
En parallèle, le service qualité peut configurer les appareils de mesure pour qu’ils récupèrent automatiquement les données de tolérance directement depuis le PLM.
Au lieu de saisir manuellement les valeurs ou de les copier, les opérateurs s’appuient sur des paramètres préchargés, garantissant une précision maximale et une cohérence en temps réel avec toute modification de révision.
La synergie entre PLM, CAM, QA et les commandes intégrées aux machines incarne l’essence même de l’intégration Industrie 4.0 : une chaîne fluide et adaptative, où une simple mise à jour déclenche un alignement instantané à l’échelle du système.
Le résultat : quasi-absence d’erreurs, gestion rigoureuse des versions, et une forte réduction des défauts de production.
Ce flux de travail exemplaire illustre parfaitement comment un écosystème numérique peut unifier la créativité du bureau d’études, la rigueur du contrôle qualité et la précision du CAM, pour aboutir à une productivité accrue et une satisfaction client
8. Passeport Numérique, KPI e JIT ↓
Dans une entreprise qui applique les principes de l’Industrie 4.0, chaque pièce ou lot est tracé numériquement tout au long des phases de production et de test.
Cela permet de créer un véritable « passeport numérique » : lorsqu’un produit final est associé à un numéro de série donné, il est possible de retracer tous les composants utilisés, les numéros de série internes, les tests réalisés et les résultats obtenus.
Chez RIMSA, par exemple, chaque fois qu’un composant subit une transformation, un numéro de série unique lui est attribué.
S’il est ensuite intégré dans un produit plus complexe, ce numéro sera incorporé dans la traçabilité finale, tout en restant consultable a posteriori.
Grâce à cette traçabilité complète, la maintenance post-vente est facilitée — il est possible de remplacer exactement la pièce défectueuse avec une équivalente aux mêmes spécifications techniques et performances — et la qualité globale du produit est renforcée.
En effet, toute anomalie peut être identifiée rapidement et isolée, limitant son impact sur les lots suivants.
Le passeport numérique devient ainsi un outil de transparence clé, à présenter aux clients et aux partenaires.
Sur le plan de la gestion, la collecte de données en temps réel permet de définir des KPI (Key Performance Indicators) clairs :
temps de production, temps de réglage, nombre de pièces défectueuses, consommation énergétique, etc.
Le suivi de ces indicateurs permet des actions correctives immédiates, l’analyse des inefficacités et la mise en place d’un processus d’amélioration continue.
Enfin, l’approche Just In Time (JIT) tire un immense bénéfice des technologies 4.0:
le système planifie la production de manière précise, en fonction des besoins réels et des cycles de travail, évitant ainsi les accumulations de stock et réduisant les gaspillages.
Lorsque le MRP indique qu’il est temps de lancer la fabrication, les services concernés savent exactement quels matériaux prélever et à quel moment, tandis que le système informatique gère automatiquement les priorités en fonction des commandes en cours et des prévisions de vente.
En résumé, le passeport numérique, les KPI et le JIT forment un triangle vertueux de contrôle, d’amélioration continue et de réactivité face aux évolutions du marché, rendant l’entreprise véritablement résiliente et compétitive.
6
Conclusions: La digitalisation comme culture d’entreprise
Le parcours de transformation numérique de RIMSA démontre que l’Industrie 4.0 n’est pas seulement une question de technologies avancées, mais bien une question de culture.
De la conception à la production, de la logistique au contrôle qualité, chaque fonction de l’entreprise doit coopérer de manière fluide, en s’appuyant sur une plateforme numérique commune et des processus partagés.
Dans cette perspective, la formation continue du personnel et la promotion d’une culture de collaboration deviennent des facteurs clés de réussite.
La digitalisation ne transforme pas seulement les outils, mais aussi les mentalités et les façons de travailler, en plaçant l’humain, la transparence et l’agilité au cœur de l’organisation.
Les avantages sont d’ailleurs concrets: meilleur contrôle, réduction des coûts et des déchets, efficacité énergétique, transparence et traçabilité à chaque étape.
Sur le plan humain, un environnement de travail digitalisé offre des opportunités de développement, stimule la curiosité et renforce l’implication des collaborateurs.
L’intégration des données et l’interconnexion des machines permettent d’améliorer la qualité de manière systématique, garantissant au client final un produit fiable, parfaitement tracé et conforme aux normes les plus strictes.
En définitive, la digitalisation n’est pas une finalité, mais un processus en constante évolution.
Pour rester compétitives, les entreprises doivent mettre à jour régulièrement leurs systèmes d’information et former leurs équipes aux nouvelles technologies, en plaçant l’innovation et la qualité au cœur de leur stratégie.
À travers son exemple, RIMSA montre que même une PME peut réussir avec succès cette transformation, en s’imposant comme leader de son secteur et ambassadrice d’une nouvelle culture industrielle.